|
Post by jeff on Apr 12, 2020 9:44:59 GMT
Hi folks. I recently purchased a really nice example of a MK1 Morris. I appreciate they are now very rare and I want to continue improving the car. A couple of problems have caused me some concern regarding suspension. The ride heights are acceptable and generally the car drives well. No pulling, just a bit floaty at speed. However at very low speed, walking pace or less, if I stamp on the foot brake there is a disconcerting "CRACK" sound from somewhere in the front suspension, offside mainly, and a "CLUNK" from the near side. I cant find anything obvious like ball joints or wheel bearing play, or any lateral movement in the suspension arms.
With the car on the ground I could get a small amount of rock "click" by pulling and pushing the top of the n/s wheel but on jacking up the car found no rock or play even with a large gemmy bar under the tyre or trying to lift or twist the suspension arms. Hmmmm??? I have recently replaced metric brake calipers with new imperial ones and pads. Everything there is properly torqued up. I'm certain the noises aren't brake pad movement. This is much louder.
With these two faults apparent, I've taken the car off the road for safety's sake in case something breaks. I have considered completely gutting the front suspension and have purchased a new Hydrolastic pump and vaccum pump in anticipation.Ive also bought a pair of new knuckle joints just in case.
I've never taken out the 1800 suspension mounting brackets before and wondering if anyone else has experienced those "CRACK" CLUNK" noises, and found a problem other than ball joints.
My thinking is leading me to upper arm bearings, knuckle joint wear. Lower arm bushes, tie rod bushes etc. Obviously I dont really want to pull it all out unless I have to but if I do then so be it. That jobs looks to be a bit of a piggy.
Any advice, pointers and work arounds will be most appreciated.
Jeff.
|
|
|
Post by Penguin45 on Apr 12, 2020 17:38:40 GMT
Given what you've looked at already, I would further have a look at the tiebars to start with. Drop the housings down and check the rubbers and the state of the metal. This is safety critical and should be checked regularly anyway. The other possibility springing to mind is the driving flange on the end of the drive shaft. These can wear and partially rotate, giving rise to clicks and clonks. No doubt more ideas will be along presently.  Chris.
|
|
|
Post by 1800heap on Apr 12, 2020 21:41:10 GMT
Hi Jeff
I Think Chris is spot on with the tie bars, That's the first place I would look. As he said you need to pull them off for a good look. Out of interest at what point do you get the noise while stopping?
Nick
|
|
|
Post by dave1800 on Apr 13, 2020 2:25:15 GMT
Hi Jeff, welcome.
As Chris and Nick have indicated it is very important to check the condition of the tie-bars' rubber bushes and ensure the lock nut is tightened to the correct torque. Ensure the condition of the "torpedo" housing is sound paying special attention to the condition of the weld holding the plate through which the end of the tie-bar passes. These welds have been known to crack and failure can lead to the lower suspension arm being forced backwards and jamming the wheel with potentially catastrophic consequences.
The reasons for this are believed to include the rubbers deteriorating leading to hammer blows and also the locknuts becoming loose and of course corrosion. In Australia there were several modifications made to try and overcome this problem. However, I think one of the main contributory factors is that they are out of sight so can be overlooked and can also be missed at MOT inspections unless there is considerable play.
The clicks when braking and accelerating again are frequently down to the front hub rotating on the splines. There are quite a number of detailed posts on this subject and it is important to deal with it as soon as possible to avoid damage to the hub components. First check is to ensure the hub nut is tightened to 150 foot pounds.
The clunk is more difficult to determine the cause as you have already checked the obvious. Before dismantling the front suspension I would suggest carefully checking engine and exhaust mountings. The suspension upper arm bearings are prone to corrode and break with age and the knuckle joints are also a not uncommon issue.
David
|
|
|
Post by foglaursen on Apr 13, 2020 8:06:08 GMT
It can be difficult to locate any play in the front suspension. I have found that depressurising the Hydolastic suspension makes it much easier. Peter 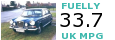
|
|
|
Post by andrewa on Apr 13, 2020 8:30:41 GMT
Hi Jeff As per above, the tie bars should be the first thing you thoroughly check. Personally I'm a bit retentive about noises and I ended up doing what you're suggesting - taking it all apart and going right through it. I did try fixing it piecemeal but on reflection it was a waste of time - if you can I'd vote for doing it all. Getting it back to "as new" transforms the driving experience and if you have the expertise or money, I'd recommend it. On mine the main culprits were the top arm bushes and the knuckle joints in the housing with the worn nylon seat making the noise.
Also you may find - I did anyway - that some parts that have been on there a long time have worn in a certain way so when you start carrying more passengers/less passengers or change one thing, it has a knock on effect! So they may look ok, behave ok when static, once underway you get those irritating noises as they're wearing on a slightly different part. Good luck with whatever you decide to do.. Regards Andrew
|
|
|
Post by jeff on Apr 13, 2020 9:28:20 GMT
Well thanks so much guys for the comprehensive and knowledgeable replies. Im glad I joined this forum. Although I spent my apprentice days fixing ancient corporation buses,and restored several BMC delights, there is always something new to learn especially about oddball vehicles such as ours. As I said, I've never taken out a full suspension unit on an 1800, and at first sight it looks daunting. I just hope I dont bust any studs holding the alloy mounting bracket to the cross tube.
As far as drive flanges go, I "think" they are ok as I dont hear any noise on the move when going from drive to overrun.
Nick's question is interesting. The "CRACK CLICK" from the offside happens at very low speed at the point of a full nose dive on stopping dead as in a very low speed emergency stop. I think the engine mountings are sound as they are relatively new including the new 2 piece set above the engine shock absorber.Having said that the steady bar between gearbox and body it worth a check.
I've read quite a lot on this sight about tie rod failures and fully understand the implications. Fortunately,that's the first part to come out but I will check the hub nut load (good idea),while the car is on the ground. Getting 150ft/lb torque with the car suspended might be difficult.
I'm frequently in touch with Tony Wood, from LOCI and we have discussed parts availability.
On balance, I think the advice given to dismantle the full assembly on each side is the best way forward and then scrutinise each part. A full rebuild although quite expensive will give me peace of mind and hopefully I wont need to revisit that job for some time. Good practice with my new hydrolastic pump kit too.
Looks like quite a shopping list for Tony's emporium!
Thanks again for the information and thought provoking advice.
Well I suppose I'd better do a little less thinking and a bit more doing and get my 66 year old bones onto the garage floor...groan!
|
|
|
Post by 1800heap on Apr 13, 2020 23:24:23 GMT
Jeff It might be worth checking your front and rear bump stops too. If the clonk happens at the lowest part of the dip when you are hitting the brakes, as you have indicated. You might have metal to metal contact instead of metal to rubber!
My car used to make a loud clonk sound similar to your description. When I rolled back on our drive, which was quite steep and used the handbrake to stop the car it made the noise. The rear of the car would come up high enough for metal to metal because of a faulty rear bump stop rubber. A missing front or rear might make this noise. You are going forward but the effect is the same. High rear, low front!
Good luck with it anyway. There is usually someone on here that can give you some pointers or the little bit of info you need to move forward. Chris and David in particular are always willing to help.
Nick
|
|
|
Post by andrewa on Apr 14, 2020 6:49:25 GMT
Morning Jeff - stock up on the Ibuprofen gel and you'll be fine, I'm sure! Think you're right - but I would say that! Once it's done, it's done and you should be able to have complete confidence in your front end for a good few years. Fingers crossed you won't find any horrors - but if you do, you wouldn't be the first! Good luck Andrew
|
|
|
Post by dave1800 on Apr 14, 2020 8:00:01 GMT
Agreed, you can also jack each front wheel in turn and insert a lock of wood between the upper suspension arm and the bump stop, then lower the wheel. This takes the load off the suspension and helps to make it easier to find any play. David It can be difficult to locate any play in the front suspension. I have found that depressurising the Hydolastic suspension makes it much easier. Peter 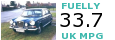
|
|
|
Post by dave1800 on Apr 14, 2020 8:08:41 GMT
Hi Jeff You may wish to look at this thread on the Oz 1800 website noiseas it relates to a MK1 car with the roller bearings in the upper suspension arm. As far as removing the aluminium housing is concerned, the bottom large bolt can be a bit of a pig so worth a good soak in penetrating fluid and be prepared to use some (or a lot of)heat to free it. David
|
|
|
Post by jeff on Apr 16, 2020 9:03:44 GMT
Thanks guys for all that info so far.
So far, I've managed to dismantle the offside suspension assembly. Luckily for me someone had been in there in the past and very thoughtfully used coppaslip on the bracket bolts. The hardest part was breaking the lower arm ball joint pin. That needed the splitter wound up as far a I could get it, several blows with a couple of hammers and a lot of heat. It sounded like a gunshot when it eventually let go.
I ended up having to cut the lower arm pin nuts to remove it as they were seized solid and rusted together with the pin. Again, lots of heat and a severe beasting to get the tapered part of the pin out of the lower arm. Luckily, Tony wood from LOCI is providing me with new lower arm sleeved bush kits, which include new pins etc.
The upper arm bearings were found to be very "lumpy". Very slack in the mid point of travel,and very tight as the arms were moved up or down from the mid point. I would think all the wear takes place in only about 25% of the the whole bearing, which to me is not an ideal application for a taper roller bearing designed to rotate. Ball joints are quite free but no undue movement found, but Tony has posted two new upper arms which already have the ball joints and bearings and tubes.
Of course, the bump stops (rubbers ) are another issue. One missing and one hanging off. And, you might know, the fixing screws were well and truly corroded into the alloy bracket causing them to snap off. I didnt want to apply much heat to the alloy so had to drill them out. Now I'll have a rummage to find suitable screws and retap the holes to whatever I can come up with.
The tie bar came off without too much difficulty. The bracket is a bit rusty but not too bad. The inner plate and weld Is sound but it's slightly bent due to the t9òop hat shaped bush being worn right through causing the tie bar to scrape the edge of the hole. I guess this would have added to the noises.
So I'm just waiting for a delivery from Tony for all the bits for both sides and then hopefully, the front suspension will be as good as new.
I'll update as I go
Cheers for now
|
|
|
Post by andrewa on Apr 16, 2020 10:36:25 GMT
Flippin' heck - when you decide to get on with something, you don't hang about! Sounds like you'll be doing the weekly shop in her by middle of next week! Cheers Andrew
|
|
|
Post by jeff on Apr 17, 2020 18:08:55 GMT
Haha andrewa. I do go for it once I'm up for it. Takes me ages to get motivated.
I'm about to put it all back on the car now its rebuilt, then do the other side.
I could do with a bit of advice from you wise men. I had a bit of a trial run getting it back onto the car today but ran into trouble trying to line up the knucle joint spigot into the displacer. I have fitted a spring in the spigot hole, which was missing. I can hardly get my fat fingers in behind the alloy bracket to line the Knuckle up. Its awkward an not exactly lightweight. I'm thinking there must be an easy way to do this but I haven't seen it.
Help please.....0
.
|
|
|
Post by Penguin45 on Apr 18, 2020 10:26:42 GMT
Assuming that you have the weight of the car still on the rear wheels, you could slighty re-inflate the suspension, which would push the connecting rod outwards and allow you to engage it in the cup on the top arm.
Chris.
|
|